Labor Health and Safety
The King Jim Group considers employee safety paramount and is working hard to improve its labor health and safety. At the KING JIM Headquarters and Matsudo Office, a Health and Safety Committee has been established. Each site health and safety general manager directs safety supervisors, health supervisors, and other personnel according to the management system.
1. Prevent employee risks and health problems.
(1) Hold regular meetings of the Health and Safety Committee (once a month).
(2) Implement stress checks (once a year) and provide information about interviews for high-stressed employees, implement these interviews, and carry out group analysis.
(3) Implement walking events in the King Jim Group (twice a year).
Call for participants to aim to walk 8,000 steps per day for one month period and share the results within the company. Participants range from employees with hobbies such as walking, running, and mountain climbing to those who generally don’t normally exercise, and the competition is rather fierce for the top rankings. Original goods featuring the design of King File-kun are provided as a participation prize every time.
(4) Implement a final office closing time of 20:05
(5) Implement no overtime days every week on Wednesdays.
(6) Issue warnings to the superiors of employees whose overtime exceeds 45 hours per month.
(7) Post and distribute early-stage response manuals and other materials for preventing the spread of COVID-19.
Photo of the activity of top-placing employee in the walking event
2. Implement educational sessions on health and safety topics for employees and so on.
・Implement lectures by labor health physicians. 3. Implement health checkups and carry out other initiatives for the promotion of health maintenance.
(1) Implement health checkups once per year.
(2) When employees have been dispatched overseas for periods longer than six months or have completed overseas work lasting six months or more, implement special health checkups for those being assigned to positions in Japan.
(3) Set up workplace vaccinations for COVID-19 and special leave for those who experience side effects.
4. Investigate the causes of industrial accidents and establish recurrence prevention countermeasures.
King Jim Group industrial accident figures for the past three years.
With zero industrial accidents group-wide as our goal, we continue to promote prevention activities by investigating the conditions in which each incident occurred.
5. Prevent illegal activities and disasters related to work operations carried out by employees and other personnel at cooperating factories.
6. Prevent accidents involving the vehicles of entering and exiting contractors such as trucking company drivers.
7. Declare a health and safety policy.
8. Investigate risk, harmfulness, and similar factors, and take measures based on the results of these investigations.
9. Draft, implement, evaluate, and improve health and safety plans.
10. In addition to the items listed above, carry out operations as necessary prevent industrial accidents.
Carry out the following as disaster prevention measures.
1. Implement disaster prevention training for new employees.
2. Implement evacuation drills, including tenants at the Matsudo Office, and e-learning fire drills in some locations.
3. Secure three days’ worth of emergency supplies at all branch locations in Japan.
4. Introduce a safety confirmation system to be used to check the safety of employees in emergencies.
5. Create a fire prevention plan and an organizational chart for regional disaster preparedness, and make employees aware of these materials by posting them on internal networks.
Labor Health and Safety Initiatives
(1) Hold regular meetings of the Health and Safety Committee (once a month).
(2) Implement stress checks (once a year) and provide information about interviews for high-stressed employees, implement these interviews, and carry out group analysis.
(3) Implement walking events in the King Jim Group (twice a year).
Call for participants to aim to walk 8,000 steps per day for one month period and share the results within the company. Participants range from employees with hobbies such as walking, running, and mountain climbing to those who generally don’t normally exercise, and the competition is rather fierce for the top rankings. Original goods featuring the design of King File-kun are provided as a participation prize every time.
(4) Implement a final office closing time of 20:05
(5) Implement no overtime days every week on Wednesdays.
(6) Issue warnings to the superiors of employees whose overtime exceeds 45 hours per month.
(7) Post and distribute early-stage response manuals and other materials for preventing the spread of COVID-19.
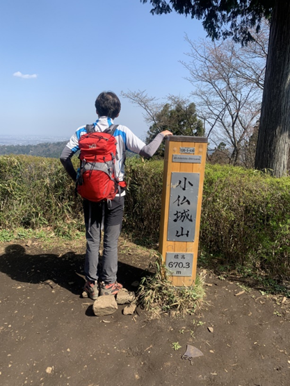
・Implement lectures by labor health physicians. 3. Implement health checkups and carry out other initiatives for the promotion of health maintenance.
(1) Implement health checkups once per year.
(2) When employees have been dispatched overseas for periods longer than six months or have completed overseas work lasting six months or more, implement special health checkups for those being assigned to positions in Japan.
(3) Set up workplace vaccinations for COVID-19 and special leave for those who experience side effects.
4. Investigate the causes of industrial accidents and establish recurrence prevention countermeasures.
King Jim Group industrial accident figures for the past three years.
Fiscal year ended June 20, 2021 | 11 cases |
Fiscal year ended June 20, 2022 | 6 cases |
Fiscal year ended June 20, 2023 | 11 cases |
Disaster Prevention Measures
- Environmental Policy
- Responding to Climate Change
- Eco-Friendly Products
- Collecting "TEPRA" PRO Tape Cartridges
- Environmental Conservation Activities
- Labor Health and Safety
- Diversity
- Human Resource Development
- Work-Life Balance
- Human Rights
- Procurementt
- Product Safety
- Local Community